Under Increasingly Strict Global Environmental Protection Requirements, the coal chemical industry, as a typical representative of high pollution and high energy consumption, is facing unprecedented environmental pressures. The wastewater generated during coal chemical production exhibits complex compositions, high pollutant concentrations, significant water volume fluctuations, poor biodegradability, and high salinity, making traditional wastewater treatment processes inadequate to meet increasingly stringent discharge standards. Efficient and economical treatment of coal chemical wastewater has become an urgent challenge for the industry. In this context, Suzhou Sulco Environmental Engineering Co., Ltd., leveraging its leading technological capabilities, extensive engineering experience, and exceptional service capabilities, has emerged as a leader in coal chemical wastewater treatment, providing efficient and stable solutions to the industry and supporting green sustainable development for the coal chemical sector.
Technological Innovation: Tackling Coal Chemical Wastewater Treatment Challenges
Since its establishment, Suzhou Sulco Environmental Engineering Co., Ltd. has prioritized technological innovation as the core driver of its development. To address the characteristics of coal chemical wastewater, the company has developed a series of innovative treatment processes covering pretreatment, biological treatment, and advanced treatment stages, effectively resolving key challenges in coal chemical wastewater treatment.
1. Pretreatment Processes: Efficient Removal of Suspended Solids and Oily Pollutants
Coal chemical wastewater contains large amounts of suspended solids, oily pollutants, and refractory organic matter. If not effectively treated, these substances severely impact subsequent biological treatment. Sulco Environmental employs high-efficiency inclined plate oil separators and dissolved air flotation (DAF) units in the pretreatment stage, combined with intelligent chemical dosing systems, significantly improving oil-water separation efficiency. The inclined plate separator increases the oil droplet surface area for faster separation, while the DAF unit injects micro-bubbles to enhance oil removal by attaching to rising bubbles. Additionally, the company optimizes coagulation-sedimentation processes using high-performance coagulants like polymeric ferric sulfate and polyacrylamide, alongside advanced equipment such as hydrocyclones, effectively removing suspended solids and colloidal substances to create optimal conditions for biological treatment.
2.Biological Treatment Processes: Enhancing COD and Ammonia Nitrogen Removal
Biological treatment is the core stage of coal chemical wastewater treatment. However, traditional biological processes struggle to achieve desired results due to the wastewater’s poor biodegradability and high ammonia nitrogen levels. Sulco Environmental introduces novel bioreactors such as Moving Bed Biofilm Reactors (MBBR) and Membrane Bioreactors (MBR) to improve efficiency. MBBR employs suspended carriers in reactors to support microbial growth, achieving biomass levels several times higher than conventional activated sludge processes. The fluidized carriers ensure full contact between wastewater and biofilms, significantly boosting COD and ammonia nitrogen removal. MBR integratesUltrafiltrationor microfiltration membranes with biological treatment, enabling high microbial concentrations and superior effluent quality that meets reuse standards.
The company also optimizes traditional Anaerobic/Oxic (A/O) and Anaerobic/Anoxic/Oxic (A²/O) processes by adjusting parameters such as reflux ratios and sludge retention times, increasing anoxic zone volumes to enhance denitrification efficiency. Total nitrogen removal rates now exceed 70%. Additionally, Sulco Environmental adopts anaerobic ammonium oxidation (anammox) technology, utilizing anammox bacteria to directly convert ammonia and nitrite into nitrogen gas under anaerobic conditions, eliminating the need for external carbon sources and reducing operational costs.
3. Advanced Treatment Processes: Degrading Refractory Organics
For refractory organic compounds and high salinity in coal chemical wastewater, Sulco Environmental employs advanced oxidation technologies (AOPs) in the advanced treatment stage. Combinations such as ozone oxidation coupled with Fenton oxidation and photocatalytic oxidation effectively degrade recalcitrant organics and reduce wastewater color. Ozone oxidation directly oxidizes organics via its strong oxidizing power, while generated hydroxyl radicals amplify degradation. Fenton oxidation utilizes hydroxyl radicals produced by iron ions and hydrogen peroxide for efficient organic breakdown. Photocatalytic oxidation leverages light-activated catalysts to generate electron-hole pairs, further enhancing hydroxyl radical production.
In membrane treatment, Sulco Environmental selects materials based on wastewater characteristics and reuse goals. For high-salinity and high-hardness wastewater, anti-fouling, salt-resistant polyamide reverse osmosis (RO) membranes are used. For organic-rich wastewater, hydrophilic, fouling-resistant ultrafiltration (UF) membranes are prioritized. The company optimizes membrane operational parameters, such as pressure and flux, to extend membrane lifespan and reduce costs.
Engineering Expertise: Delivering Customized Solutions
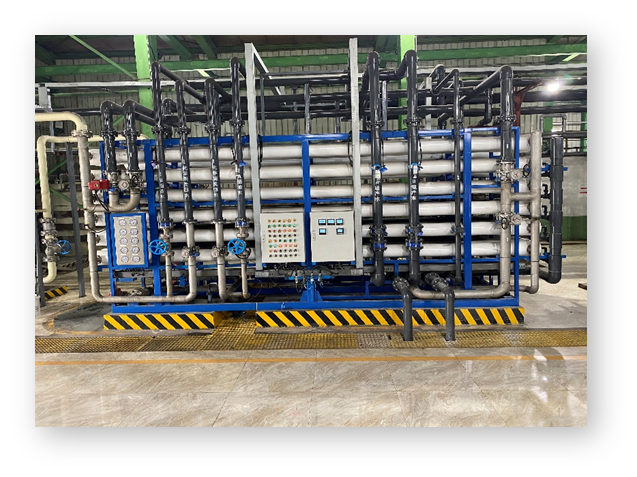
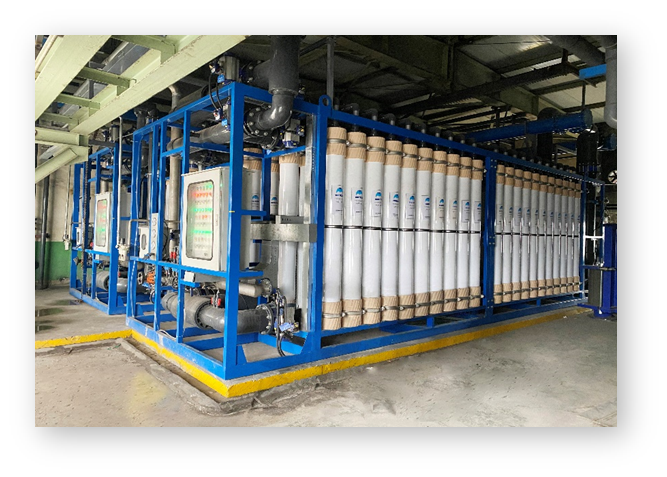
Suzhou Sulco Environmental Engineering Co., Ltd. combines cutting-edge technology with extensive engineering experience. The company provides tailored wastewater treatment solutions based on clients’ production processes and wastewater characteristics, offering end-to-end services from design and construction to operation and maintenance for both new projects and facility upgrades.
In a real-world case, Sulco Environmental designed and built a comprehensive wastewater treatment system for a large coal chemical enterprise. The wastewater contained high concentrations of phenols, ammonia nitrogen, and cyanide, posing extreme treatment challenges. By optimizing pretreatment, integrating MBBR and MBR bioreactors, and combining AOPs with membrane processes, Sulco achieved effluent quality meeting China’s Grade 1A discharge standards. Portions of the treated water were reused in production, enabling water recycling and significant cost savings.
Driving Green Sustainable Development
Suzhou Sulco Environmental Engineering Co., Ltd. adheres to the philosophy of “technology-driven, green development,” committed to delivering efficient and economical wastewater treatment solutions for the coal chemical industry. Through innovation and engineering excellence, the company not only ensures regulatory compliance but also promotes water recycling, advancing the sector’s green transformation.
Looking ahead, Sulco Environmental will increase R&D investment to explore more advanced and cost-effective technologies. Plans include developing bioaugmentation techniques to screen and cultivate microbial strains specialized in degrading refractory organics and high ammonia nitrogen, improving biological treatment stability and efficiency. The company will also focus on membrane material modification and fouling control to enhance the economic viability of membrane processes.
Suzhou Sulco Environmental Engineering Co., Ltd.—a pioneer in coal chemical wastewater treatment—remains dedicated to technological innovation, driving industry progress, and collaborating with partners to build a greener future.
Suzhou Sulco Environmental Engineering Co., Ltd.—The Leader in Coal Chemical Wastewater Treatment, Partnering with You for a Sustainable Tomorrow!